Laser Drilling & Inner Contour Cutting
Creating the Perfect Hole
Laser glass drilling is a dry and contactless process introducing through holes or cut-outs into glass sheets with very low glass chipping and hence high edge strength as well as extremely high precision - in terms shape and positioning accuracy.
Laser glass drilling is based on laser ablation using green laser light (532 nm). Usually, glass absorbs light in the far IR and UV wavelength region and is highly transparent in the visible wavelength range. Therefore, it seems surprising that green laser light can be used to process glass when only a very small fraction of the laser light can be transformed into heat. Glass is a so called wide-bandgap material where the photon energy of normal solid-state lasers at 532 nm is not high enough for a direct single-photon bandgap excitation of the material.
However, if a laser beam is strongly focused into the glass material and at the same time the laser pulse emission is very short, a high intensity energy distribution is achieved that exceeds the so called threshold intensity at which the material absorbs the green laser light. This effect is called non-linear absorption and effectively enables laser glass drilling with green laser light.
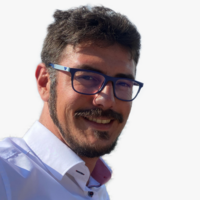
JobShop - Laser technology as a service
Through our JobShop, we offer you the chance to benefit from 4JET's high-tech equipment for laser drilling of glass without having to make the initial investment for your own laser processing systems. Our MicroFab location in Prutting near Rosenheim not only handles all production steps from initial sampling to 100% quality control, but also the procurement of substrates, cleaning and packaging as well as door-to-door logistics.
If you are interested in perfect glass edges by precision laser systems, here you have the opportunity to gain first experience with the quality of the process.
For more information about our laser processing service, please contact us at any time or visit our JobShop website.
Guiding the beam through the glass
Not only the strong focusing of a short pulsed green laser beam into the glass, but also the guidance of the focus within the material is essential for the production of a through hole or cutout in glass. To create the hole, the laser beam is focused into the back of the glass surface and moved upwards, allowing the vaporized material and glass particles to flow freely in the opposite direction, away from the processing zone.
This prevents the interaction between the laser beam and the material vapor, resulting in higher drilling performance and precision. When the focus reaches the upper glass surface, the drill core is released and falls out of the hole. A suction nozzle below and above the glass removes the vapor and glass particles.
Laser ablative glass drilling summarized
- The process offers a high degree of design freedom and allows holes and inner contours to be freely shaped.
- Laser drilling is also suitable for processing thin glass.
- The resulting chipping is small compared to mechanical methods, and high-quality drill hole edges are achieved.
- Precise positioning creates high quality products that cannot be produced by mechanical methods.
Contact
We look forward to your questions – our experts are at your disposal.